Lost Wax Bronze Casting
Creation of Your Bronze Sculpture | Creation of Your Gift Box | Printing Your Certificate
We use the ancient art of Lost Wax Casting, as detailed below, to cast your sculpture in solid bronze metal. Every time we cast a piece, a new mould is created and subsequently destroyed. This means that every single piece of sculpture bought from us is entirely hand made and utterly unique, which is why it is numbered by hand to tell you which casting of the edition you have bought.
1. Mould Making
A silicone rubber mould is made of the original art work. Absolutely every detail captured or missed by this mould will be reproduced in the bronze castings. Depending on the size of the mould, it may then be cut into sections for casting.
This is the master mould used to originate all castings of that piece. Each time that piece is ordered, we follow the following procedure:
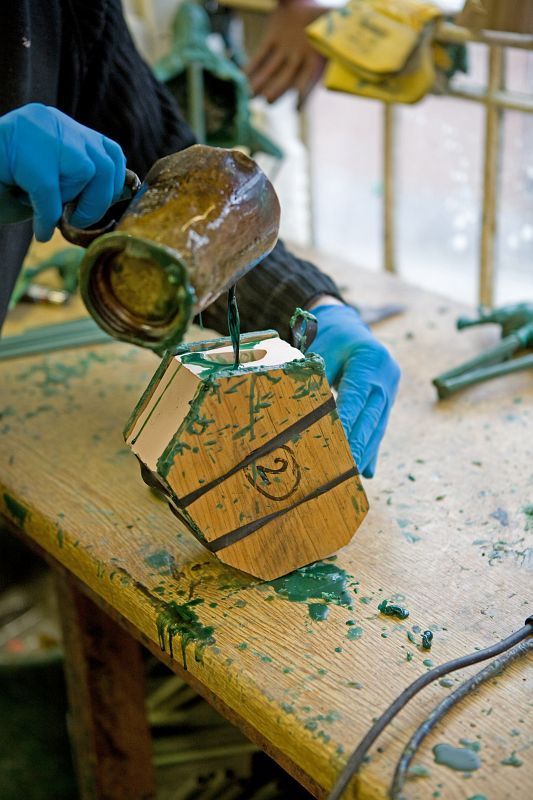
2. Making the Wax Casting
Molten wax is poured into the rubber to create an exact wax duplicate of the original model.
3. Chasing the Wax
The wax is removed from the rubber mould any flaws are hand finished by a skilled craftsman.
4. Spruing
Wax rods and a wax pouring cup are carefully attached to the wax casting in just the right positions to allow bronze to be poured in any displaced air to escape. This means that no air bubbles are trapped inside the mould as they would be gaps in the finished bronze piece.
5. Investment
The wax model with attached rods is now covered in ceramic material which will form the mould for the final bronze pour. This is done by dipping the wax model carefully into investment liquid and then covering it in a fine powder before allowing it to cure (completely dry). The model is then dipped into investment liquid again and given a coating of a coarse ceramic powder. By following this procedure several times, a ceramic shell is built up around the wax model.
6. Burn-Out
The wax inside the ceramic shell is then placed in a kiln and fired. The shell bakes and the wax is melted (lost) from the shell. This creates a hollow ceramic shell mould and accounts for the term "Lost Wax" being applied to the process.
7. Casting
The ceramic mould is removed from the kiln and molten bronze is immediately poured into it, at 1200°C.
8. Break Out
Once the casting has been allowed to cool for several hours, the mould is carefully removed by hand from the bronze model inside.
9. Sandblasting
Any fragments of the ceramic shell are removed by sandblasting and the sculpture is carefully inspected at this point.
10. Assembly
All attached rods and cups (which are now bronze) are removed by hand. At this point, any segments of a large sculpture that has been cast in sections are welded together.
11.Chasing
All the weld marks and removed and rod marks are chased and re-detailed by hand. Any scars left by the rods are carefully blended to match the rest of the sculpture’s surface as intended by the artist.
13. Patination
The bronze is first heated before the chemical patina is applied by an artist. A patina can achieve many different colours or effects depending on the mix of chemicals used.
14. Waxing
Finally a wax coating is hand applied before the piece is polished to ensure a beautiful lustrous patina.
15. Numbering
Finally, the piece is numbered by hand. It is numbered as the casting number, followed by a slash and finally the edition size. For examples, 5/250 means that your piece was the fifth piece to be cast from the master mould out of 250 castings made. The piece also bears the signature of the artist. Jonathan Sanders pieces are all marked with a JS or JRS. Sue Maclaurin pieces are marked either Sue Maclaurin, Sue Mac, or with her insignia of an S and small cat face.